個別受注生産業態におけるデジタルスレッドの必要性
一般的に組立製造業の生産業態には「個産」と言われている「個別受注(設計)生産」と「量産」と呼ばれている製品群およびビジネスモデルが存在しているかと思います。本稿のテーマである「個別受注(設計)生産」は、図1に記述している通り「量産」型の生産形態よりも製造リードタイムが一般的に長いことが特徴であり、一旦製品のオーダーとして確定された後で製造オーダー(製造指図)を出した後にも、上流側の設計変更がどんどん入ってくるというような特徴があります。
また「量産」とは異なり、実際の現場では非定型の製造業務が多く、明確な作業指示が非常に重要となります。そもそも一品一品構成も違うので明確な作業指示をデジタル情報で出し、指示内容の変更があったらこれもデジタル情報として変更し、その変更した最新の製造指示情報に対してもデジタル情報として製造実績を入れるというところが重要となります。
その他にも厳格な形態管理、いわゆるAs-Buildということでこの製造指示に対して実際にどういうもの(どの部品番号のどのシリアル番号/ロット番号)で組み付けたのかという、As-Build BOMの記録を残した上でサービス部門にも連携し、その情報がサービス業務にも活用され、その後にAs-MaintainedのBOMとして連携できることが非常に重要です。
厳格なトレーサビリティということで、単なる製造だけのトレーサビリティだけではなく設計から起こった設計変更が工程設計にきちんと反映され、それが電子作業指示にどのように指示され、その指示に基づいた製造作業の記録というものを作業記録と品質記録含めてしっかり情報として格納されている、しかも途中で仕様の変更や不適合や特採などさまざまな外乱が起こった場合においても、きちんと記録が取れていなければいけない、というそもそものニーズや特徴がある業態であるのが「個別受注(設計)生産」です。
図1: 個別受注(設計)生産業態の特徴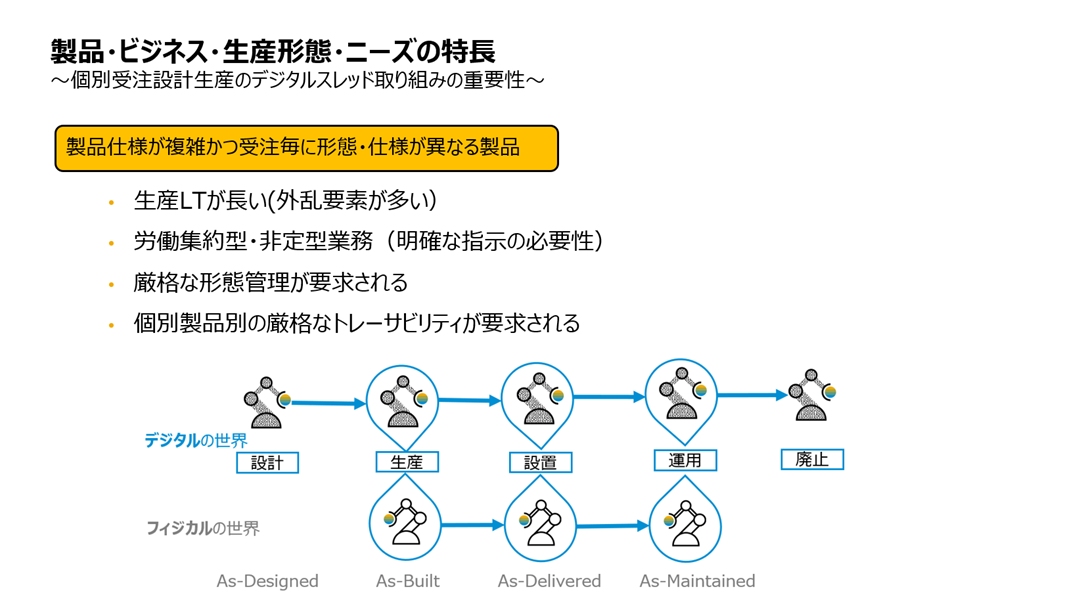
そういった意味では、「量産」の業態よりも、上流の設計情報をミスやロスすることなく、切れ目なく下流の製造部門までデジタルな情報を糸(スレッド)のように連携・情報活用し、上流で起こりうる設計変更の情報についてもヌケやモレなく、製造現場まで伝達していくという設計-製造、すなわちエンジニアリングチェーンとサプライチェーンの間の蜜連携がより一層求められる業態であります。
図2: 個別受注(設計)生産業態の課題と解決の方向性
さて、先ほどよりエンジニアリングチェーンとサプライチェーンが連動し、上流から下流までデジタル情報を活用していくということが特に個産のビジネスでは重要であるという話をしておりますが、実際にはいろんなお客様においては図2の左図に記述されているような課題があるのではと思っております。
具体的には関連する部門で別々のシステムが点在していて、情報が連携されておらず、サイロ化されているために、何とかその連携を保とうと人間が間に入って様々な情報を検索したり、別のシステムに情報を転記したり、転記内容を確認したりといったような本来システム連携がなされていれば不要なはずの付帯業務に工数がとられていたり、それでも時間をかけてでも人が転記した内容がミス・ロスなく登録されているとまだいいのですが、実際には人間が行う作業になるために、どうしてもこの部分でミス・ロスが発生し、そこで手戻りが発生したり、場合によっては、正しい情報が反映モレになっているということで本来は不要であるはずの古い部品に手配がかかっていて過剰在庫になったり、逆に製造現場に必要な新しい部品が供給されておらずに機会損失につながってしまうというということが起こりうることかと思います。
また特に個産ということで、一旦製造指図が作成されてからのリードタイムが長いということで、製造作業の途中の段階で設計変更が起こったならば、その部品変更が影響する製造指図を特定したうえで、その製造指図を一旦ホールドして製造作業を止める必要がでてくると思うのですが、システム的に連携がなされていないということで影響範囲の特定に時間がかかり、その間にも製造活動が進んでしまい、あとからやり直さなければいけないリワーク作業が増加し、場合によってはその部品やユニットまで製造してしまった場合にはその部品やユニットそのものが使われないものとして除却損として計上しなくてはいけない可能性も出てくるかと思います。
その他にも、ある意味では1製品ごとに異なる構成部品を扱うために、製造現場にも本来であれば正しい製造指示書を提供し、製品組み立て時に実際に使用した部品のシリアルやロット情報をインプットしようにも、そもそも誤った(まだ変更内容が反映されていない)製造指示のまま組み立ててしまうということになれば、製品品質の問題にもつながりかねません。
こういった個産特有のエンジニアリングチェーンとサプライチェーンの連携・融合における現状の問題を解決する方向性としては、大きく考えると以下の3つの方向性が必要ではないかとSAPでは考えております。
- 上流のPDMシステムからシームレスに部品情報を下流のERPに連携させ、さらに現場向けのMESともつながる、理想を言えば少なくともPDMからの変更情報を単一のシステム上で反映・管理できるようなフローやプロセスの構築
- 変更情報の影響範囲分析と場合によっては実際の製造指示をホールドさせるには、単にマスタデータの影響範囲ではなく、その先にあるトランザクション(実際にはMRP実行からの製造指図)情報まで含めた影響範囲の特定ができる仕組みの構築
※これはすなわちマスタデータとトランザクションデータを管理しているERPにしかできない部分かと思います。 - さらにその一旦ホールドした製造指図に対して、途中で起こった設計変更の内容を伝搬できるような設計変更管理から製造指図への変更管理プロセスの構築
課題解決のための3つの方向性に対するSAPソリューション
SAP S/4HANAでは先ほどの3つの方向性を目指す際に必要となってくる機能について、以下の図3に記述されている黄色枠の3つの機能を使ってサポートすることができるのではと考えております。
1.上流のPDMシステムからシームレスに部品情報を下流のERPに連携させる
- この部分をつかさどるのが、SAP PDM Integration機能となります
2.変更情報の影響範囲分析と場合によっては実際の製造指示をホールドさせるには、単にマスタデータの影響範囲ではなく、その先にあるトランザクション(実際にはMRP実行から製造指図)情報まで含めた影響範囲の特定ができる仕組みとなります
3.さらにその一旦ホールドした製造指図に対して、途中で起こった設計変更の内容を伝搬できるようなEBOM・MBOM設計変更情報の反映から指図への変更管理プロセスの構築
- 特に後段の2つについては、PPの機能を拡張しているSAP Product Engineering & Operation(通称PEO)と変更レコードという機能の組み合わせで提供することになります
図3: 個別生産向けのデジタルスレッドをサポートするSAPソリューション
結び
いかがでしたでしょうか。特に製造リードタイムが長く、製造途中の段階でもあっても変更を反映する必要がある個別生産の形態においては、設計-製造部門のエンジニアリングチェーンとサプライチェーン間で密接な連携がより必要となり、デジタルスレッドの必要性がでてくることを解説させていただきました。また本稿では各SAPソリューションの詳細にまでは紙面の関係上ハイレベルでの対応ソリューションの有無についてのみ記述させていただいておりますが、こちらの個別生産業態に向けたデジタルスレッド機能やその詳細にご興味を持たれた方は、ぜひSAPの担当者までご連絡いただければと思います。