Logistics is the science of making thing A and delivering it to point B, and has been described as the calling card of America.
“Until the pandemic arrived, we lived in a vast, elaborate, whirring contraption that delivered culture and commerce at spectacular speeds, with astonishing efficiency,” wrote the author of a New York Times article earlier this year.
What happened to the great American logistics machine? It fell apart. Back in March, 75% of companies had already reported that COVID-19 had disrupted their supply chain. Companies that chose not to invest in their supply chain in previous years either crashed or suffered a severe hit this year due to lack of resiliency. Even companies with highly rated supply chains did not escape unscathed.
What Went Wrong
According to the Harvard Business Review, the challenge for companies after the pandemic subsides will be to make their supply chains more resilient without weakening their competitiveness. Before the pandemic, manufacturers in most industries depended on suppliers and subcontractors that narrowly focused on just one area. Those specialists, in turn, usually relied on many others. The advantages of this arrangement include flexibility in what goes into the product as well as the ability to incorporate the latest technology. But relying on a single supplier somewhere deep in its network for a crucial component or material leaves manufacturers vulnerable.
In a recent discussion, Takshay Aggarwal, group lead for IBM Digital Supply Chain, and Darcy MacClaren, senior vice president of Digital Supply Chain for SAP North America, discussed reasons for supply chain failure and talked about the IBM and SAP partnership, which offers a truly transformative road map for supply chain excellence.
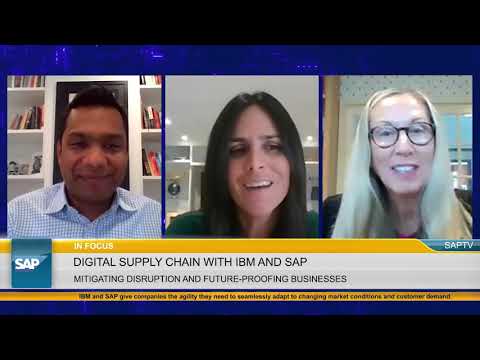
Aggarwal spoke about logistics problems during the pandemic. “There’s a lot of logistics transformation going on right now,” he said. “Supply chains broke down because in their efforts to save dollars, companies were single sourcing things. They didn’t have alternatives. And when there were fluctuations, they were not able to accommodate them with alternatives such as other transportation lanes.”
He explained that companies were not prepared for shifts in demand, such as selling to more grocery stores rather than to restaurants. Grocery retail requires different packaging and different types of transportation. Local optimum does not mean global optimum. It is not enough to have islands of excellence in each function, so enterprises are moving toward intelligent workflows, which are more agile by nature. Aggarwal believes companies will have to look at their overall logistics strategy, from carrier network rationale to their ability to react to change.
What Needs to Change
MacClaren said data has been one of the biggest stumbling blocks for most enterprises, because they store massive amounts of data in different silos.
“Lack of visibility into real-time data greatly hampers a company’s predictive capabilities,” she explained. “All our customers want to improve their ability to predict the future. And if that’s not possible, then they want to improve their response.”
MacClaren believes the best way for suppliers to meet the challenge is by putting the customer at the center, then organizing to deliver the perfect experience through a multichannel, multimodal supply chain.
Both experts agreed on the two key factors behind the collapse of supply chains: lack of agility and the inability to respond in real time. One factor preventing agility is the use of disparate systems. “If you have to pull all the information you need for analysis from different points, and then you have to do it again and again, it really slows you down,” MacClaren said. “Folks just didn’t have visibility to do their job. True agility depends on the interoperability of systems.”
They also agree on the critical factors for recovery. Companies should begin by figuring out what part of the process is most broken. While it is important to create a holistic journey for transformation, every supply chain has its own needs depending on the industry and the customer. In addition to applying technology to the supply chain, companies also need to facilitate cultural change. This is where the concept of intelligent workflows, rather than individual processes, plays a key role.
Win-Win for Customers
Aggarwal sees a huge opportunity for the Internet of Things (IoT) and the use of artificial intelligence (AI) for demand sensing and forecasting. “IBM has always been on the cutting edge of emerging tech;,be it blockchain, AI, or IoT,” he shared. “By combining SAP’s industrial scale enterprise solutions with IBM’s new, most promising technology, we can drive that exponential value for our customers.”
For MacClaren, the SAP and IBM combination of intelligent technologies and a truly transformational road map of where to go is what can make the difference for future supply chain excellence. Now is the time to prepare, she said, so those “vast, elaborate, whirring contraptions” really do deliver culture and commerce at spectacular speeds, with astonishing efficiency, even amid a global crisis.
Listen to more episodes of In Focus.
Follow me on Twitter: @magyarj