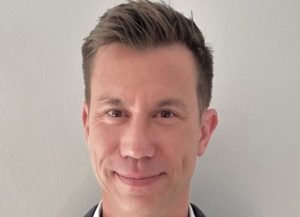
This development recognised that to drive high performance in the face of increasing complexity and uncertainty, businesses need tools and functionalities that are honed for their specific industry.
To identify, contain and recover from an unexpected occurrence with speed, for example, requires decision making abilities that only a relevant industry solution can deliver.
Domain expertise in a particular industry such as agriculture, mining, or pharmaceuticals, can help the organisation to easily identify any concerns, bottlenecks, errors, and other problems, and provide faster resolutions.
This is leading to a rise in demand from industry verticals, with many businesses wanting the functionality and workflows that a pro forma implementation cannot provide.
“Some business sectors are unique or complex, with regulatory compliance that requires tight control over processes and conformance,” says Andre Adendorff, Director Presales at Seidor Africa, an SAP Business One partner.
“Food and beverage manufacturing is one such case. It is a complex and labour-intensive industry and when compared to other manufacturing sectors, has its own challenges.”
Manufacturing efficiency
Food and beverage companies require efficiency in the business and throughout the supply chain.
Having an ERP system that is relevant for the needs of food manufacturers ensures that factors like material requirements planning, inventory management, and recipe control function properly.
Food ERP systems provide everything a business needs to perform core food and beverage functions, including:
• Inventory and supply chain management
• Quality control and quality assurance
• Non-conformance management
• Process automation
• Recipe management and ingredient tracking
• Batch control and traceability for regulatory compliance
• Cross-functional reporting
Product safety
When processed foods maker Tiger Brands detected a leak in certain canned vegetable products due to a faulty side seam weld, the company was quickly able to recall 20 million cans.
“In this industry, manufacturers of all sizes must be able to respond quickly and effectively to the recall of products deemed unsafe or unsuitable for the market, as the consequences for not doing so can have long-term deleterious effects, in legal, financial and reputational terms,” says Adendorff.
“In the age of social media, a company’s reputation can be destroyed in an instant should it not respond appropriate to any issue associated with product safety.”
With recall functionality and built-in controls to preclude product recalls from happening in the first place, industry-relevant ERP solutions enable companies to better prepare for, prevent and minimise product recalls, limiting potential damage to the business.
Meeting needs of demanding customers
When it comes to food and beverages, consumers today are more health-conscious than ever about what they choose to consume, and what effects their choices have on the planet.
Their purchases are often strongly determined by nutritional value, packaging, and shelf-life. They want to know what is in the food they buy, which creates an increased demand for transparency in product labelling and food safety.
“This increases costs in an industry that already has tight margins,” says Adendorff. “To mitigate the impact of these demands, ERP for the food and beverage sector makes it easy to track information and meet the requirements for compliance with food safety regulations, both in South Africa and abroad.
Food safety management
Companies that export food and beverages abroad are required to meet amongst others, FDA FSMA and the BRC Global Standard for Food Safety, a Global Food Safety Initiative (GFSI) benchmark, which means it’s accepted by many of the world’s biggest retailers.
Achieving the certification ensures that consumers have confidence in the products. BRC contains requirements for food processors to follow to build an effective food safety management system that includes full traceability.
“Food-relevant ERP’s that can account for all processes is essential for companies that need to meet regulatory requirements – as well as those of other food safety compliance and regulatory bodies – helping manufacturers ensure full compliance and deal with non-conformance,” says Adendorff.
“An ERP system can schedule and manage production, assuring quality control. It can also manage non-conformance and corrective action requests for audit purposes.”
The software can be configured and installed in a way that constantly benchmarks against standards. It assists with streamlining and automating processes, saving considerable time for employees and management.
“Having software to monitor, measure and analyse product quality and delivery helps to reduce waste and inefficiencies throughout the business,” Adendorff adds.
“This has a positive impact on productivity and can help to boost the bottom line, even in a tough economy.”