Paper manufacturer Steinbeis produces around 300,000 tons of recycled paper every year. But it is operating in a hotly contested market and to continue offering competitive prices and producing paper sustainably, the company is aiming for cost efficiency through digitalization – with SAP HANA.
At its factory near Hamburg, family-owned Steinbeis produces an annual 300,000 tons of office paper, magazine paper, and digital printing paper from recycled paper. It began the switch from using wood pulp to using 100 percent recovered paper as the raw material for its paper production back in 1976.
“It was a breakthrough innovation at the time,” says Ulrich Feuersinger, managing director of Steinbeis Papier GmbH. “In those days, paper manufacturers were focused more on obtaining low-cost raw materials than on what their environmental impact might be. But, as a sixth-generation family-owned company, we enjoy the advantage of not having to think in terms of quarterly results. When it comes to growing our company, we can take a longer-term perspective.”
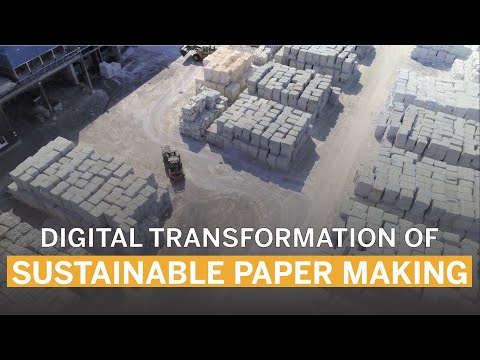
Digital Transformation for Efficient IT
Today, Steinbeis is a leader in the sustainable, closed-loop manufacturing of recycled paper. As a midsize company, it faces fierce competition from larger rivals. “In Scandinavia particularly, we’re up against competitors that source their raw materials from managed forests,” Feuersinger explains. “We have to be better and faster than them, which is why having efficient IT systems is key to our survival.”
Three years ago, Steinbeis began expanding its digital transformation in production across the entire company. “Industry 4.0@Steinbeis Paper,” a project supported by avato consulting ag and SAP, is the first major step on this journey.
“We’ve been using SAP software in all the production processes at our paper factory for 20 years now,” says Dr. Michael Hunold, head of New Processes at Steinbeis. “We’ve already achieved a high degree of digitalization and automation in production. But we realized that there was a lot of data we could only analyze in retrospect. That gave us the idea of having all that data analyzed automatically in the background.” This is the focus of the Industry 4.0 solution Steinbeis is implementing across the board.
“Our aim from the start was to turn information into insight in seconds,” Hunold says. “We want to transform data into knowledge and use that knowledge to reap strategic and operational benefits. SAP HANA is the solution that’s helping us achieve that aim.”
In conjunction with its strategic partner for the initiative, avato, Steinbeis translated its ideas into use cases for specific applications and defined the technical set-up. SAP HANA, with its broad functional portfolio and unique features, forms the core of the tailored solution avato delivered to Steinbeis to collect data from production, the manufacturing execution system (MES), and the SAP ERP application and analyze it using state-of-the-art machine learning algorithms.
“Avato implemented our queries in applications that capture the relevant data from SAP HANA, prepare it, and deliver it to us as actionable insight,” explains Hunold. What that means in practice is that every single second more than 25,000 sensors on the production line deliver data, which is then analyzed on the SAP HANA platform in conjunction with data from the MES and SAP ERP in near real time.
“From the operational perspective, our aim is to supply paper with consistent quality features and to do so cost- and eco-efficiently,” Hunold shares. “We can only do that if our technical processes are stable at all times.” For Steinbeis, this includes learning from the experience of past incidents in production.
“Thanks to our fully digitalized production lines, we can monitor our processes automatically and at high speed,” says Hunold. “So we now have the technical capabilities to respond to incidents early and avoid production downtime.” Incidents typically include unusual machine behavior, excessive energy or raw material consumption, and product quality issues.
“Our aim is to maximize machine availability because the information we receive in real time means that we can resolve incidents without losing precious time,” he says.
SAP HANA: Informed Decisions in Real Time
Steinbeis has connected more than 25,000 sensors to its central database, SAP HANA. The data these sensors deliver is organized and analyzed by avato’s Smart Data Framework. Combining the integrated functions in SAP HANA for data management and analysis with powerful machine learning algorithms, the solution helps ensure that monitoring is seamless and entirely automated.
“SAP HANA is a super fast database – and that’s exactly what we, at Steinbeis, need,” says Hunold. “When I run an analysis, I don’t want to have to wait hours for the results. If there are inconsistencies in product quality, for example, I need to know immediately.”
“With SAP HANA at the heart of our Smart Data Framework, query response times on large volumes of data are typically less than one second,” says Wolfgang Ries, managing director of avato consulting ag. “Other key benefits of SAP HANA are its extremely high data compression ratio and the fact that it supports both the traditional relational data model and graph data models in a single, integrated application. We map the asset structure, production processes, business processes, and so on in graph data models as digital copies – all in SAP HANA, with just 256GB RAM.”
Steinbeis is using the new platform not just for the applications in production, but also for innovative solutions throughout the company. Together with avato consulting, it has successfully implemented use cases in purchasing, materials management, and management accounting. Others are being planned.
“Thanks to SAP HANA, we can now complete our day-to-day tasks incredibly quickly,” says Torben Link, head of Purchasing at Steinbeis. “By digitally transforming our purchasing processes, we’re profiting from new possibilities that we simply never had before. We can perform mass data analyses and get genuinely actionable insight from them.”
From chemicals to a magazine paper line, all the relevant data is now monitored and captured. “Having a better overview of how much we’re spending – and where – allows us to devise new purchasing strategies,” Link says. “We can analyze how our suppliers are performing and adjust our negotiating stance accordingly, which saves us money.”
Sustainable Business in Times of Crisis
Having digitalized processes means that the purchasing staff at Steinbeis can work from almost anywhere – an invaluable advantage in times of crisis. According to Link, “Going digital has made us more resilient. When a crisis hits, we can continue focusing on our standard processes without neglecting others.”
Earlier this year, the Steinbeis project won an SAP Quality Award in the Innovation category.
Ramin Mirza, head of Platform Sales at SAP, describes the “Industry 4.0@Steinbeis Paper” project as a stellar example of what the SAP initiative #GiveDataPurpose is all about: “Data is becoming an increasingly important asset for businesses. But at the end of the day, its value depends on how much there is of it, how it is used, and – naturally – its quality. #GiveDataPurpose encourages companies to look at how they can access the right data and information from a central repository in real time to make well-informed decisions faster. Steinbeis did just that, designing a digitalization strategy that will give it a vital edge over its competitors.”
According to Steinbeis’ Managing Director Feuersinger, the circular economy is rapidly becoming a must in today’s society. “It doesn’t just save energy and resources; it encourages people to think more carefully about how raw materials are used and consumed,” he says.
His company’s raw material is recovered paper – not wood. “We use significantly less energy and water to produce our paper than manufacturers of comparable paper made from fresh fibers. We reuse waste paper, so trees aren’t being felled directly for our products.” Steinbeis also has much lower CO2 emissions than its competitors.
The company has plans for further digitalization going forward and launched a Web shop in early 2020. “We want our communication with customers to be digital in the future, too,” Feuersinger says. “Direct communication is what our customers expect, and it’s also a way for us to open up new sales channels.”
“The key to our strategy is this: all the data from our paper factory is now available on one technology platform rather than – as in the past – in two separate places, production and the SAP world,” Hunold explains. “Our Industry 4.0 project and SAP technology have given us the infrastructure we needed. We now want to use that infrastructure for any process in paper manufacturing, paper sales, and raw materials procurement. That’s the challenge we’ll be tackling next.”
Find out more about the #GiveDataPurpose initiative.