Thanks to consumer concern about the environmental impact of their favorite brands, companies are focused on producing more sustainable products and implementing processes to prevent materials from going to waste.
Currently only a fraction of our plastic waste – 14%, according to a report by the World Economic Forum and the Ellen MacArthur Foundation – is collected and recycled after use. The rest ends up in landfills or in the oceans and waterways, contributing to global warming.
At the same time, new regulations and policies are being established, such as extended producer responsibility (EPR) regulations. These regulations help ensure that producers are responsible for the recycling, reuse, or disposal of their products. Additionally, impending plastic taxes being proposed in Europe that apply to plastic packaging produced or imported that do not contain a specified amount of recyclable content.
This is great news for the planet, but the new scenario creates a market-by-market challenge, especially for large producers, as it is very difficult to manage product regulations across different geographies. In fact, managing thousands of products and materials across hundreds of regulatory systems in multiple regions is one of the greatest complexity challenges facing global brands in the years ahead.
According to new regulations, companies are required not just to design products and packaging to eliminate waste and pollution. They also must keep materials in use at its highest value for the longest possible period of time. The bottom line is that companies will need to base future decisions on sustainability and recyclability. This change is driven by consumer demand, the availability of technology, and the new regulatory environment.
Manufacturers embarking on transformational journeys are often challenged by complex supply chains, heavy assets, and legacy technology. They must also transition to new business models that require a circular approach to product design from the outset and new approaches like reintroducing the product or its materials back into the manufacturing process at the end of the life cycle.
The SAP Responsible Design and Production solution responds to the drivers behind the change and helps businesses tackle these challenges.
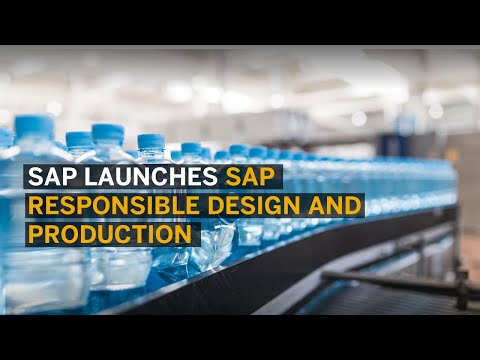
Stephen Jamieson, global lead for Circular Economy Solutions at SAP, says the new solution will help enterprises tackle this complexity as they move away from a take-make-waste linear economy to a circular one designed to eliminate waste, circulate materials, and regenerate natural systems.
“The solution is designed to help enterprises comply with regulations,” he explains. “It’s currently focused on packaging and plastics, but it will be further developed as different material categories such as batteries or textiles come into scope for regulatory intervention.”
The complexity begins with the roughly 400 different regulatory schemes that are currently in place or planned around the world.
SAP Responsible Design and Production is, first and foremost, about tackling the complexity of packaging regulations and new taxation regimes. This helps brands to accurately assess and calculate those implications, use these insights to inform how products and materials are designed, and optimize these choices. This collaboration is crucial, together with non-governmental organizations (NGOs) and partners, in accelerating the transition to a circular economy.
Investing for the Long Term
Extended producer responsibility won’t come cheap. Jamieson cites the example of the UK, where one study predicts a cost of £2.7 billion per year for post-consumer packaging waste. The UK scheme incentivizes producers to design packaging that is easy to recycle and helps ensure that they pay the full net cost to manage this packaging once it becomes waste, in line with the polluter-pays principle behind the EPR concept.
That is the cost in the UK alone, which represents three percent of the world. “Do the math, and you’ll see the global impact,” says Jamieson. “Some of the larger manufacturers produce thousands of tons of materials each year. In these markets, you’re talking about very meaningful numbers. And don’t forget the plastic taxes, which tally up to £250 per ton in the UK and €400 a ton in the European Union.”
That may sound like a high price to pay, but the benefits outweigh the cost. Visionary enterprises like Unilever find that short-term sustainability costs can lead to long-term savings. According to the company, it has cut costs by US$1.5 billion since 2008 by improving efficiencies in factories and using fewer materials.
In the long run, the EPR approach encourages innovation in product and packaging design. Reuse and recycling consume less energy than manufacturing from new materials. As the costs of collection, processing, and recycling are shifted from taxpayers to the producers of the materials, enterprises will find ways to cover the EPR costs through savings in other areas.
How It Works
SAP Responsible Design and Production helps businesses manage EPR regulations and prepare for upcoming plastic taxes, a benefit for companies that want to get a head start on meeting their responsibilities
As an example, the solution is designed to enable EPR experts at large global consumer products companies to accurately calculate the packaging fees and meet packaging regulations for a particular market. These experts must understand what declarations are necessary then ensure that they are reporting accurately to those bodies. They must assess the data, understand any exceptions and challenges to the data quality, and ensure everything is codified properly according to regulations. The solution then enables EPR experts to draft an assessment of the policies and fees at play, and finally, to run a formal declaration that will be used as the basis of the company’s payment to the relevant authorities.
An overarching analytics layer allows category managers to see the projection and the implications of different regimes on their product portfolios. This offers a more strategic view for people like chief sustainability officers to see progress toward commitments, such as the elimination of problematic or unnecessary single-use packaging.
Jamieson concludes that SAP Responsible Design and Production is essentially an extension of enterprise resource planning (ERP) — something SAP has been leading for 50 years — with an additional element. “Now, we’re not only planning the optimization of resources; we’re optimizing them to be regenerative.”
Natasha Pergl is lead for Global Circular Economy at SAP.