Weidmueller is a German company with a longstanding history as a leader in the field of “industrial connectivity” – the kind of connectivity envisioned by Industry 4.0, where smart factories use data and connectivity to drive new heights of manufacturing efficiency and productivity.
Based in Detmold, Germany, the company prides itself as a “progressive thinker and trailblazer” that offers solutions that allow producing companies to prepare themselves for the Industrial Internet of Things (IoT). These solutions enable safe production control from the cloud – without the need to completely modernize all machines in the factory. This offers customers an affordable approach toward incremental Industry 4.0 adoption – an approach that many manufacturers are eager to explore.
Early on, Weidmueller recognized the potential of Industry 4.0 capabilities for its own manufacturing processes and decided to take advantage for its own digital transformation initiative and lead by example in the industry it serves.
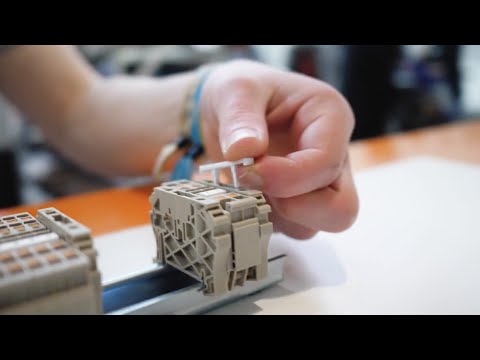
Dr. Patrick-Benjamin Boek heads up the digitalization and factory IT team at Weidmueller. “What we aimed to do is to embed intelligence into the factory floor to eliminate paper, improve transparency, reduce waste, and boost the efficiency of our machines and workforce,” he said.
Weidmueller’s approach was to integrate SAP Digital Supply Chain solutions for digital manufacturing with its existing SAP technology landscape. Boek and his team focused on Weidmueller’s molding department as a pilot. Just four months after launching the project, the company went live.
Weidmueller’s implementation generates more than 300 data points that give employees on the floor the information they need to optimize production and maximize productivity.
“We were able to cut downtimes up to 50 percent, as our employees on the shop floor now have accurate insight into machines,” Boek said. This has enabled the company to boost overall machine efficiency – which has, in turn, helped to increase the value of the company’s investment in capital equipment.
With its implementation partner Syntax, Boek’s team also developed native iOS apps that enhance usability on the shop floor by enabling staff to access information in real time on iPods and iPads. “We’ve eliminated the time spent walking to each machine to check on status,” Boek shared. “This has helped us increase efficiency by up to 20 percent and cut manual effort by up to 60 percent.”
Better insight into cycle times and other key performance indicators (KPIs) has helped Weidmueller improve performance, optimize allocation, and make better decisions. And with automated processes that increase transparency into machines and equipment, the company has been able to speed delivery times as well.
“With Industry 4.0 and the Internet of Things (IoT) we now have a fully integrated digital manufacturing and process landscape,” said Boek. “With help from SAP solutions for digital manufacturing, we’ve been able to maximize the overall efficiency of our machines and improve experiences for our customers.”