SAP was at Hannover Messe, the world’s largest trade event for industrial manufacturing, to demonstrate its leadership in digital supply chains and its broad portfolio for end-to-end business processes. Members of the Executive Board of SAP SE Julia White, chief marketing & solutions officer, and Thomas Saueressig, head of SAP Product Engineering, attended in person.
Speaking on the opening day of the trade show, Saueressig said, “Exceptions are now the rule. Today’s globally networked supply chains are especially prone to disruptions – with far-reaching consequences for the manufacturing industry. Flexibility and agility are needed to react quickly to changes.” Adding her impressions of SAP’s presence at the event, White said, “It’s an amazing collection of both SAP technologies and our broad partner ecosystem, and it is us working with our ecosystem that’s solving our customers’ challenges.”
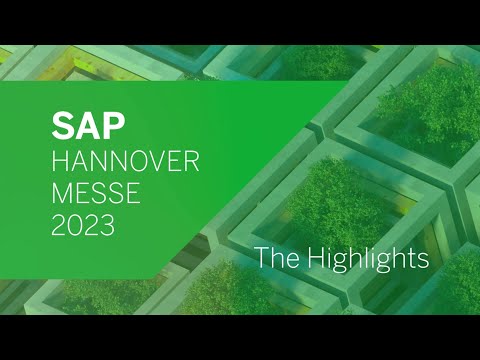
SAP Solutions in Action
There was certainly plenty for visitors to take in at SAP’s booth, from showcases and guided tours to live sessions and partner stands.
SAP is striving to help shape digital transformation in manufacturing. And one of the most pressing questions for that industry today is how to make production and supply chain processes resilient and sustainable.
To answer that question, SAP gave visitors ample opportunities to try out SAP solutions and experience them live in action in a “demonstration factory” it had at the trade show. The show booth “factory” was a partial sample of SAP’s recently opened Industry 4.0 Pop-Up Factory innovation center at the company’s headquarters in Walldorf, Germany. Attendees were able to view the rest of the factory remotely from SAP’s booth or through virtual reality glasses in its “Industrial Metaverse” showcase.
On Display: How SAP Solutions Manage Supply Chains and Manufacturing
SAP also demonstrated systems that support production operators in a part of multi-stage production in which a component is assembled for the end product. In a scenario focusing on in-process quality control, SAP showed how operators receive precise visual instructions during the assembly of an electronic control head, guiding them through the process and reducing errors. It also explored the value of embedded artificial intelligence (AI) in quality assurance, showing how image recognition technology can be used to check how likely it is that parts have been assembled correctly and whether they have any defects. A highlight here is a kind of digital birth record, which can be thought of as a finely structured documentation of the production process. All relevant data from machines, as well as input from users, is recorded there and assigned to an individual product.
Also in the spotlight were applications for digital twin solutions, not just for virtual models and real-time simulations but also for human-machine interaction. Visitors were able to learn more about this from the example of autonomous mobile robots that independently pick up parts from a warehouse and – rather than placing them on a conventional conveyor belt – take them straight to a modular station.
SAP also showcased an augmented reality solution for production operators. Here, personnel wearing smart glasses receive instructions and feedback on whether they have carried out a work step correctly directly in their field of vision.
Digitally Mapping and Managing the Entire Production Process
Hannover Messe attendees could also try their hand at remotely controlling and monitoring the Industry 4.0 Pop-Up Factory in Walldorf, viewing a live, end-to-end production line for mixing and filling liquids as used by the process industry in the manufacturing of chemicals, pharmaceuticals, and consumer goods.
The demonstration showed that one central control room is all that is required to control and monitor production across locations. SAP calls this control room a “production control center.” Commenting on this live factory session, Matthias Deindl, head of SAP’s Industry 4.0 Center EMEA & India, said, “This scenario shows companies how SAP can help them have a full overview of everything that is happening on the factory floor – not just planning, but managing the entire production process for batch manufacturing.” In the future, it might even be possible to create a purely digital version of the control room in the metaverse. Companies could then design and operate it exactly as they wanted. And they would no longer need to house it in a brick-and-mortar space.
In the scenario shown in Hannover, the production line is connected to SAP Digital Manufacturing. All the information needed to fulfill the production order – including the customer’s specifications – is sent seamlessly to the machine. The process is paperless and can incorporate customer requirements without manual intervention. Another function of the production control center is to monitor the production line and key performance indicators, such as process efficiency, scrap rates, and good parts produced, as well as the current condition of the machines and equipment.
Cloud Solutions Enable Vertical and Horizontal Integration
One of the highlights at SAP’s booth was the electric CNC injection molding machine that let visitors track the production of their own customized cup – from top floor to shop floor in the production hall. This pop-up production station, staged in cooperation with SAP partners Fanuc and Syntax, demonstrated how SAP Digital Manufacturing can integrate a highly automated machine and control manufacturing.
Starting with order planning, visitors chose from various configuration options on a monitor. They could select a color or color combination for their cup and specify which logo it should have. The SAP software then dispatched the order to the machine electronically and production of the cup began using recycled and recyclable plastic. Visitors could take the cups they made home with them.
While visitors were creating their cups, sensors were capturing a range of key information about the machine’s condition and how many good and defective parts had come off the line. This shows how in a real-life setting, the seamless flow of information also works in reverse, meaning from the machine level back to the office level. Data like this can be analyzed in SAP Analytics Cloud, giving customers valuable insights to help them optimize the production process.
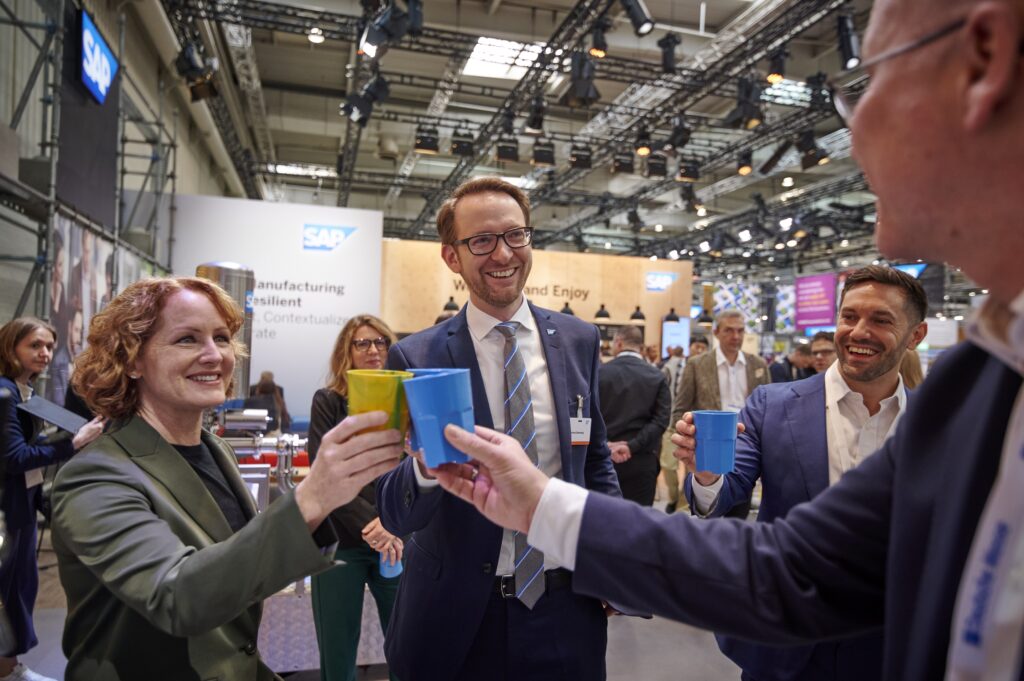
Resilient, Efficient, Sustainable – and Profitable
Visitors to SAP’s booth could experience the full product life cycle – from design and planning, manufacturing, logistics, and installation to operations and maintenance. They learned how the processes at each of these stages can be optimized by, for example, embedding AI to integrate them horizontally.
Vertical integration can also connect all levels inside the company. Linking manufacturing and business processes in this way eliminates data and knowledge silos. “Here at Hannover Messe, we’ve brought everything together under one roof to demonstrate realistic end-to-end scenarios,” said Ralf Lehmann, Solutions Management Digital Manufacturing & Industry 4.0 at SAP.
Businesses want to ensure that their manufacturing and logistics operations are efficient, cost-effective, and reliable. Yet they must also meet profit and sustainability targets. “Manufacturers are facing two major challenges right now. One is the ongoing disruption to supply chains. The other is sustainability, which has become a top priority for CEOs. If you consider that only 7% of global economic output today is circular, then the opportunities are huge,” says Saueressig.
At its booth, SAP showed how it is one of the world’s leaders not only in enterprise resource planning (ERP) but also in digital supply chain. Industry 4.0 can transform business processes from manufacturing through to supply chain. As an ecosystem that enables companies to connect, SAP Business Network also helps improve transparency. These capabilities can be used in a circular economy to foster sustainability and capture carbon emissions data. As White points out, “One of the most important things we see here is the focus on sustainability. Creating a true network around that is how we’re going to change the game.”
Building on the network theme, SAP partners had booths nearby showing Catena-X and Manufacturing-X, the latest initiative to emerge from an alliance between industry and the German government. Here, too, SAP will play a leading role in driving digital transformation in manufacturing supply chains. Like Catena-X, Manufacturing-X will be an open and collaborative data ecosystem. Shared standards will enable data to be exchanged worldwide in compliance with European practices and data protection laws.