When the Department of Fisheries challenged the industry in 2015 to find new solutions for farming fish in the open seas, Norway-based Nordlaks Oppdrett AS stepped up and won the competition based upon an innovative and sustainable approach.
The family-owned company has been a leader in aquaculture in Norway since its founding in 1989, with comprehensive operations from breeding premium Atlantic salmon to sales and marketing. However, continuing its robust growth depends on adopting new and sustainable production methods, as space within fjords for traditional net-pen farming is limited.
Nordlaks realized that the answer lay in economies of scale and designed a unique sea vessel called Havfarm, which is currently the largest floating structure in the world. To put it in perspective, it is almost the length of four football fields and is designed to have a lifetime of at least 25 years without the need to bring it into a dry dock for maintenance and repairs.
“To keep up with growing global demand and support sustainable farming, we recognized the opportunity to turn to the open seas to expand production,” explained Bjarne Johnsen, project manager of Havfarm at Nordlaks. “We realized that the answer lay in economies of scale. If we built larger containers, we would no longer be restricted to the calm waters of the fjord and could afford to deploy more robust materials and sophisticated safety measures.”
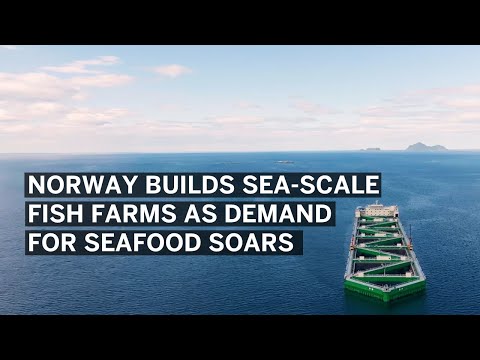
Leveraging IoT Sensors and Cloud Processing in Operations and Maintenance Processes
It is not only the sheer size of Havfarm that is impressive, but also the technology that empowers it.
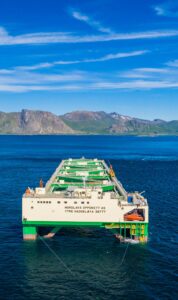
To take salmon aquaculture to a new level, Nordlaks looked to the latest technology to support operations and maintenance processes. It strategically placed Internet of Things (IoT) sensors on the vessel to monitor, analyze, and broadcast motion data in real time. This data is used to run the digital twin model of the vessel in SAP Enterprise Product Development, a cloud-based solution that can enable improved and streamlined processes for monitoring operations and maintenance.
This monitoring system enables Nordlaks to focus inspections and maintenance activities on critical areas of the vessel structure, identified through digital twin technology and virtual sensors. It measures the integrity of the structure under adverse conditions to ensure everything from the longevity of the materials to the grip of the mooring. Furthermore, heat maps are used to monitor feed output, ensuring that there is no lasting impact on the environment.
The company now has access to historic and near real-time data and actionable insights, leading to improved decision-making. It can monitor the balance of the vessel to improve ballast operations. And now it has processes in place to support efficient feed spill monitoring and simplified soil sampling underneath the vessel required to meet strict compliance regulations.
“Everything we do needs to be sustainable and that means when we leave an area, there should be no trace that we were ever there,” said Johnsen. “SAP Enterprise Product Development helps us monitor the Havfarm vessel infrastructure and environmental impacts on the seabed, which is key to our strategy for sustainable growth.”
Request a free trial and watch an overview video to learn how to enable fast, collaborative product development and lifecycle management with SAP Enterprise Product Development.
Karin Fent is senior director of Global Customer Success Digital Supply Chain at SAP.