“Finally a ‘real’ trade show again!” The heavy sigh by the organizers of Hannover Messe 2022 during their advance Internet-based announcement of the live event seemed to mark a kind of awakening – and at the same time expressed the industry’s desire to return to normality. After all, the event had to be canceled in the two previous years.
Logistics Problems Are a Drag
As such, many exhibitors traveled to Lower Saxony’s capital city with mixed feelings this year. Would industry professionals return in droves? And how would business develop?
The industry association VDMA says Germany’s machine manufacturers are enjoying a “very large order backlog.” But in an interview with the German Press Agency (DPA), Gunther Kegel, president of the German electro and digital industry association ZVEI, warned of the impacts of COVID-19-related shutdowns in China. The weeks-long break will “send a shock through global supply chains whose consequences will only be seen in six to eight weeks’ time. There’s still quite a bit in store for us,” he said.
Currently, experts cannot predict how long the worldwide logistics problems will last, making it all the more important to make supply chains as robust as possible and prepared to mitigate risks in the long term. Resilience and sustainability were among the most-discussed themes at Hannover Messe and were a particular focus of the technology companies that had a presence at the show.
Vertical and Horizontal Integration
At the Hanover show, SAP concentrated on showcases and product presentations for the discrete and process industries – and on showing how Industry 4.0 processes pave the way toward becoming customer-centric, robust, sustainable enterprises.
“Industry 4.0 empowers sustainable business processes and robust supply chains by connecting the dots,” said Thomas Saueressig, member of the Executive Board of SAP SE, SAP Product Engineering. At the vertical level, for example, machine data is being linked with business processes. Horizontal integration along “design to operate” supports improvements in the production of goods, for example, helping to avoid waste, he said.
Using the example of producing bottled milkshakes, SAP demonstrated what this can look like in a specific use case at its Live Forum. In the presentation, the company showed how the SAP system examines the sustainability of the various product components, including packaging, and points out the potential consequences based on the current product features.
A plastic cap, for example, can incur additional fees in product distribution in many countries. Insights like this are very helpful for companies that want to make their manufacturing processes more sustainable and implement more responsible product designs.
The Live Forum also served as the stage for a number of customer presentations from industrial practice – for example, to illustrate how digitalization and business transformation are virtually two sides of the same coin in times of Industry 4.0.
Sascha Rowohl, head of IT at Schwarz Production, showed how the Schwarz Group of retailers (Lidl, Kaufland) implemented its digital coffee roasting facility in just 18 months with SAP’s help. The fully automated factory was designed as a greenfield project and is slated to expand its production capacity to around 50,000 tons of coffee by the end of this year. That accounts for around 10% of all coffee produced in Germany – all of which is sold in the group’s own stores.
Among other solutions, Schwarz Group implemented SAP Digital Manufacturing Cloud, SAP Extended Warehouse Management, SAP Intelligent Asset Management, and SAP Analytics Cloud as part of this project. Connectors link the solutions with the group’s SAP ERP system. According to Rowohl, the Schwarz Group intends to digitalize more factories for other product groups step by step. An interesting aspect of these plans: the group has established a new business unit with Prezero, a disposal company, which gives the group the ability to extend its value chain from production all the way to waste recovery.
Art and a Big Show
Tangible examples like the presentation of the digital coffee roasting facility attracted considerable interest among the trade show audience. After a halting start in the morning of the first day of the show, the exhibition halls slowly began to fill up. The Meta Cube at the entrance to SAP’s booth was a real eye-catcher: a cube filled with colors and artificial light, in which a robotic arm from KUKA wrote IT terms – such as “Business Transformation” – on a transparent mirror. This installation was certainly the most photographed motif in hall 4.
Another big audience draw was the theater area (“Gate to Walldorf”), where visitors could observe the interaction between machine processes and software controls in a live stream. The scenarios were set up in Building 21 of SAP’s headquarters and were transmitted virtually to SAP’s booth at the Hanover trade show. SAP employees in Walldorf explained the presented sequences step by step, while hosts at the SAP stand took questions from the audience after the presentation.
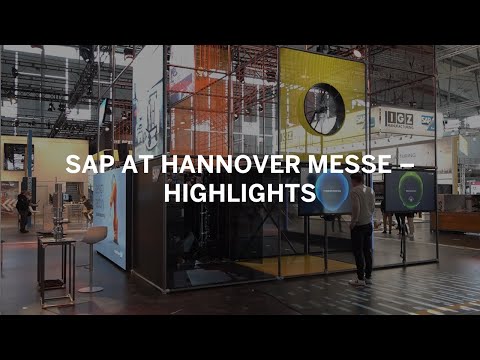
Selected partners complemented SAP’s exhibition with their presence at the company’s booth in hall 4. One of them was Catena-X, an open ecosystem where business partners from all areas of the automotive industry – including smaller suppliers – will be able to contribute in the future. The goal of this project is to seize the opportunities of digital transformation with the help of a standardized, connected data infrastructure along future value chains. According to Dr. Florian Patzer from Fraunhofer – like SAP, one of the driving forces in the network – 11 application areas have already been defined, including maintenance, quality management, and sustainability.