Just when global supply chains were recovering from the impact of the global pandemic, they were grounded by a mega-ship. The blockage of traffic through the Suez Canal by the Ever Given, one of the largest container ships in the world, showed once more how fragile global supply chains are.
Considering around 12% of global trade runs through Suez, it is not surprising that the impact is being felt even before the recently stranded ships reach their final destinations. The expectation of delays and shortages has already driven the prices of energy and consumer goods up.
The pandemic has made us aware of SAP’s leadership role in making supply chains resilient and sustainable. Lesser known, however, is that nine of the 10 largest shipping companies run SAP solutions.
Based on this collective expertise, we asked Sabine Hamlescher, chief product owner of SAP Logistics Business Network, and Till Dengel, head of Digital Logistics Solution Management, about the current challenges for shipping companies and how SAP solutions are helping supply chains become more resilient.
What crossed your mind when you saw the container ship blocking a major commercial waterway?
Dengel: It makes clear how interconnected everything is and shows the importance of logistics resiliency to global trade. Even before the Suez Canal incident, we had a shortage of containers and congestion in commercial ports triggered by the pandemic. This just adds to the pressure on global commerce. Supply chain management has been focused so much on driving efficiency that there is almost no room for failure. Goods like chemicals and automobile parts supplied from China have delivery windows of only a few days. A production stop when a slot is missed is costly for everyone.
Hamlescher: A man-made disaster turned the world’s largest ships into floating warehouses, and even the shipping companies sometimes don’t know what’s in the containers. I can imagine some CEOs are getting very nervous not knowing if their goods are aboard, let alone when they will arrive at their destination. The fact is, there’s not yet enough transparency in the logistics and transportation industry to find out. But SAP has the solutions.
How involved is SAP in serving global logistics customers?
Dengel: As the market leader in digital logistics, we are deeply immersed in supply chains across all major industries. There are more than 1,000 customers using our transportation solution, and several thousand across the logistics space, including warehousing. We manage the supply chains for many leading companies in many sectors, including consumer products, chemicals, and fashion — and I’d bet that many of them are nervously waiting for goods aboard those ships. In addition, we also serve the liner shipping side, supporting ocean freight operations for some of the largest shipping companies in the world.
Last year was the best year ever for our transportation management solution. We continue to see a strong focus from customers in solutions for solving routing and scheduling problems and for improving logistics visibility, like SAP Logistics Business Network.
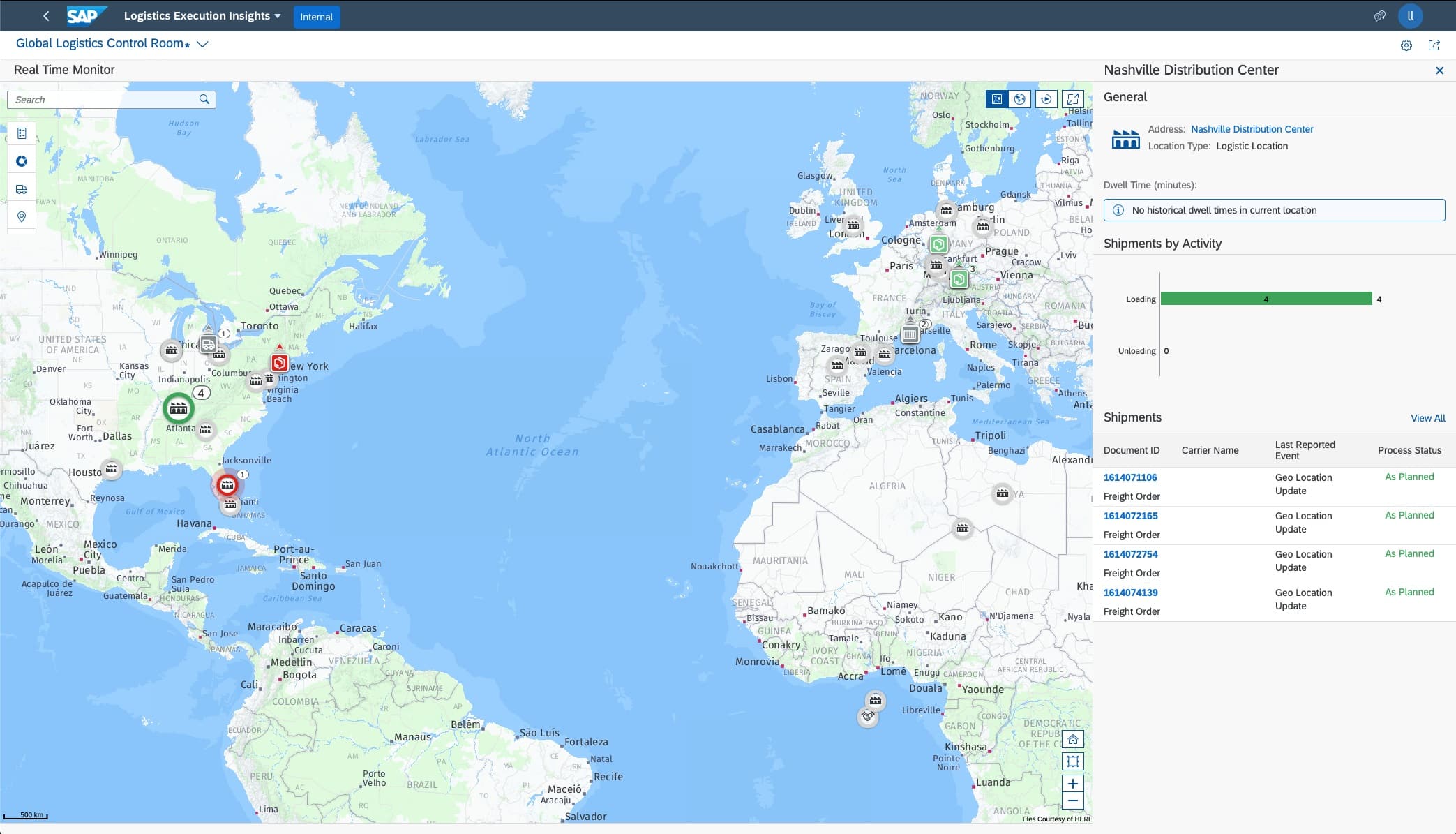
How are SAP solutions able to support the industry during a crisis like this?
Hamlescher: We have been approached by many customers for a solution to address exactly the kind of problem this event triggered. In the coming weeks we will announce new intelligent insights capabilities as part of SAP Logistics Business Network, which helps companies gain insight into all current shipments and how they are likely to be impacted by interruptions like the one playing out. Customers currently testing the beta release like that they can determine if there is an impact and then choose alternatives based on which parts of their business are affected.
The Ever Given is maneuverable again. Everything is going to be fine, right?
Dengel: Not by a long shot. The queue of hundreds of ships waiting to enter the canal will be reformed at major container ports like Rotterdam and Hamburg. Once they are unloaded, a mad scramble will ensue to transport the containers to their final destinations.
There are two dimensions to this – transportation planning and empty container repositioning. SAP Transportation Management can help rescheduling of transport from the port to the final destination. Since everyone is trying to find a trucking company that can deliver the containers, there is also a freight collaboration capability enabling customers to tap into the spot market to find a carrier in times like this of extreme scarcity. Take, for example, our partnership with Instafreight, which is like Uber for the freight industry in Europe and is connected into SAP Logistics Business Network.
The other constraint is empty-container repositioning, because there will most likely be an imbalance between Europe and China for a while. SAP Transportation Resource Planning can help reestablish stability in an optimal way.
What is SAP’s next move in logistics and freight?
Hamlescher: We continue to foster partnerships with the pioneers in logistics and container tracking technology to provide real-time visibility into supply chains. Paired with supply chain risk and operational data, we create a powerful data layer to help logistics professionals assess the impact and react to disruptions like the one we just witnessed.
Dengel: Over the past 20 years, it’s been all about efficiency and squeezing out the last cent in cost, but now the vulnerabilities have been laid bare and it is most certainly leading to a change of thinking leading to even stronger digitalization efforts. With the new RISE with SAP offering, we provide every customer access to SAP Logistics Business Network. Together with our ecosystem of partners we also created solution packages enabling customers to move from analog paper-based transportation management to a digital solution in 90 days.
Does the Ever Given incident have a message for us?
Dengel: Everything that we put into place during the COVID-19 crisis can be applied to this short-term incident. In 2020 we refocused our solutions and messaging, appealing to companies to prepare for the next crisis by making their supply chains more resilient, more digital, and more transparent. The same message applies to man-made disasters like this one.
Hamlescher: Despite the negative impact this is having on the global economy, it is a confirmation that we at SAP are working on the right topics to deliver solutions that our customers need. We have a great opportunity to help companies better navigate natural and man-made impacts to global supply chains.
This article first appeared on the SAP Global News Center.