For the industrial manufacturing industry, the seven principles of lean production are critical enablers of everything from reducing operational complexity to increasing workforce productivity and empowering a culture that values continuous improvement.
But as IT operations grow more complex, the effectiveness of lean business practices begins to diminish.
What if lean principles were applied to IT implementations too? Could deploying a defined set of technology capabilities and delivering it to specific users through the cloud streamline the software landscape and minimize complexity?
Recently, I worked with an international company on the financial functionalities of intelligent, cloud-based enterprise resource planning (ERP). Together with the customer, we discovered a better and faster way to assess and respond to the valuation of its materials inventory in a public cloud environment.
Setting a Lean Foundation for Material Inventory Valuation
With the assistance of SAP Advisory Services, the industrial manufacturer kicked off this lean ERP approach with a defined set of critical requirements for material inventory valuations conducted by its finance organization. A digital architecture and road map design service provided the advice and guidance needed to plan the transformation of business process architecture with intelligent tools and services. Such provisions ranged from linking postings to the right customer accounts to valuating materials with precision.
Through this process of self-reflection and planning, the manufacturer and SAP experts worked together to define the risks of their existing and future material valuation practices.
- Quantity risk:The basis for assessing the write-down for the span of inventory depletion.
- Technical risk:Inventories become technically obsolete due to the presence of defects or new technical developments from the business and its third parties. The existence of technical risk should be assumed if material reworking is required before the productive use of the manufactured item(s). For example, a long period of storage is often associated with an increase in technical risk.
- Price risk:The lower of cost or market (LCM) method calculates whether price risk exists. If the LCM value equals recognized costs, the inventory is not devalued. But if it matches the net realizable value, price risk is assumed.
- Management judgment:The managerial decision-maker selects certain materials and excludes them from the standard automatic risk calculation. Rates are written in a custom table and an allowance is created accordingly. In this case, quantity, technical, and price risks are not applied.
Knowing that best practices for material valuation call for a particular sequence and immediate posting of results, the industrial manufacturer chose the SAP Innovative Business Solutions organization. Together, they designed, delivered, and now run a finance application that leverages the right capabilities – and only those capabilities – based on a lean ERP approach (see figure 1).
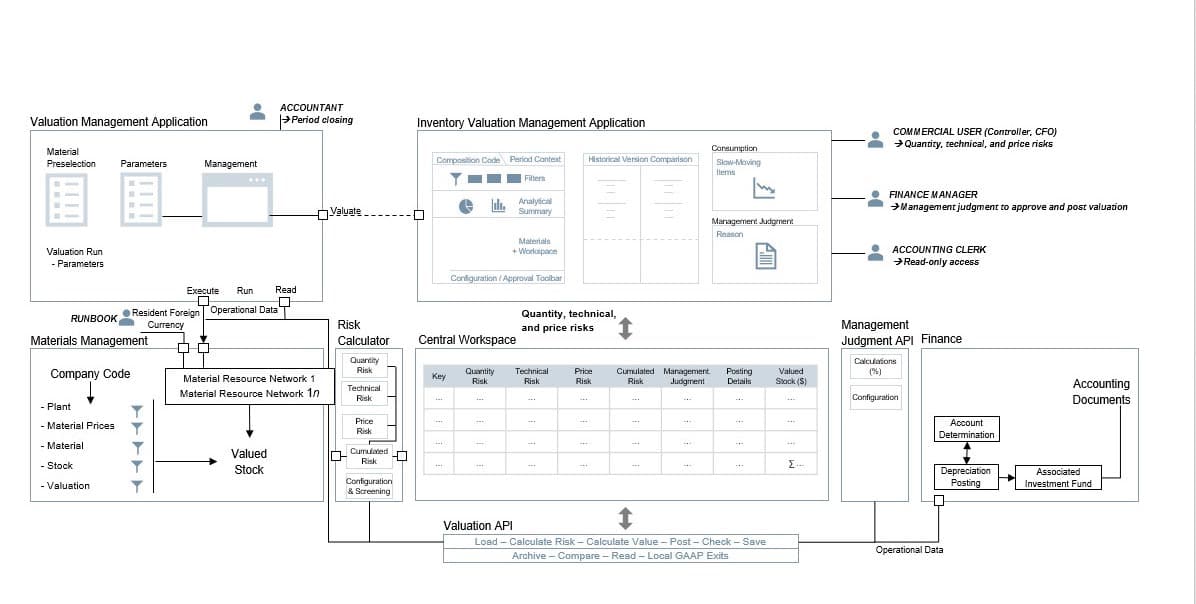
The finance application was designed with two main components:
1. On-premise backend supported by SAP solutions
During an on-premise transaction, a primary material resource network is used to determine the range of coverage for materials. To minimize the number of materials to be processed and limit the processing time within month-end operations, not all materials will be selected. For example, a pre-selection program triggers the network to process materials with a value over a predefined limit – anything less remains untouched.
In the parameters of the valuation management application, the selections are set. Since the primary material resource network runs only in a simulation, data is not warehoused. Instead, a user exit stores the data in a custom table. A core data service view pushes the data logic from the application server to the client-side and the database and exposes it through on-demand data services.
2. SAP Cloud Platform
With SAP Cloud Platform, data is stored, risks are calculated, and even values are displayed and changed. The data can then be pushed and warehoused on premise.
This platform supports two applications:
- Valuation management:All parameters for material valuation are maintained; for instance, the selection of data or considerations for technical risk.
- Inventory valuation management:Data generated by the valuation of different risks are displayed and can be changed according to financial guidelines.
Both applications run productively and comply with guidelines such as policies for logins, user authorizations, archiving, and documentation.
Reshaping Inventory Valuation Through IT Simplicity
Many industrial manufacturers are moving to lean material valuation methods based on the rate of inventory reduction. However, as we learned with our customer’s lean ERP approach, the process cannot be fully optimized without a simplified IT landscape.
By combining the expertise, best practices, and tools from SAP Advisory Services and SAP Innovative Business Solutions, our customer supports its business users with a better user interface in the cloud while minimizing traditionally inherent risks during the process. In return, its workforce has a transparent overview of material inventory, enabling better decision-making and empowering employees to act swiftly and strategically.
For our customer, this is only the beginning of the journey to lean ERP-based operations. What is next? Side-by-side innovation development for provisioning learning content and opportunities.
Stay in the conversation by following SAP Digital Business Services on YouTube, Twitter, LinkedIn, and Facebook.
Meinrad Hauser is a principal business solution architect at SAP.